USP <800> Compliance Guide for Independent Community & Retail Pharmacies | R.J. Hedges & Associates
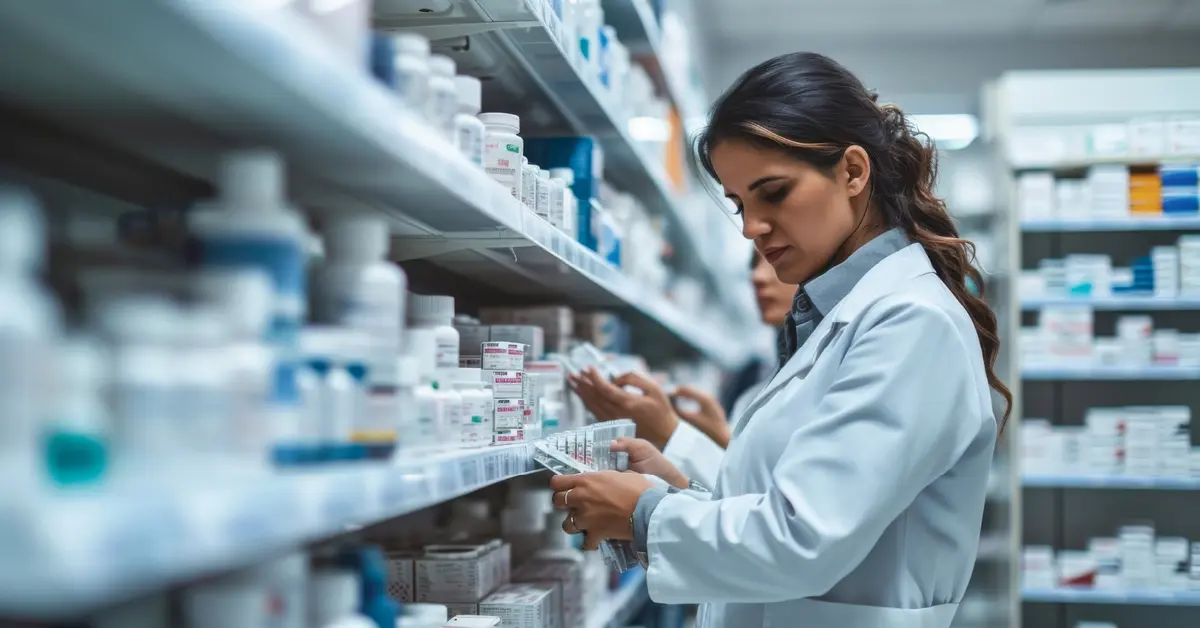
Independent pharmacy owners are no strangers to evolving regulations and industry standards. Two key areas that have seen significant changes in recent years are Hazardous Drug (HD) compliance and compounding compliance. To navigate these updates effectively, it's crucial to stay informed about what's happening in your field. Let's break down the essential points you need to know on changes to USP <800>.
USP <800> Standards and Enforcement
As of November 1, 2023, the FDA is requiring all State Boards of Pharmacy to enforce USP <800> standards. That’s right, across the country USP <800> is fully enforceable by the State Board of Pharmacy. These standards bring some vital changes:
The Evolution of USP <800>
USP <800> initially went into effect on March 14, 2020, but enforcement was optional at that time. Some states delayed implementation, but those states have gradually started incorporating it into their pharmacy inspection checklists.
The FDA has now mandated that state boards of pharmacy enforce USP <800> standards. State boards have been trained by the FDA to ensure compliance, underlining the necessity of adhering to these standards.
Retail Compounding Changes
Retail compounding, was previously permitted on retail counters. Compounding will now require dedicated areas, such as separate labs or workbenches.
All Hazardous Drug (HD) compounding MUST be completed in a Negative Pressure Lab.
There's still some uncertainty regarding specific practices like mixing two fluids, such as magic mouthwash, that may depend on specific state requirements. Reference California where altering the state of a product is considered compounding and there’s even the possibility that adding flavoring to medication will now be considered compounding.
What's Changing in Compounding?
Several changes to USP <800> are pertinent to independent pharmacies when it comes to compounding. Three of the major changes relate to beyond-use dating, dedicated spaces, and accreditation requirements. It will be important for you to fully understand these changes.
1. Beyond-Use Dating
Beyond-use dating has undergone significant alterations. Testing for batches is no longer required, but the specifics of beyond-use dating are complex. It's crucial to understand these intricacies to remain compliant.
2. Dedicated Spaces
Compounding facilities must now have dedicated spaces, especially for compounding HDs, which includes a negative pressure room(s), that must be regularly tested and equipped with alarms to monitor temperature, humidity, and pressure changes. The pressure in these rooms must be continually monitored and maintained to ensure safety.
3. Accreditation Requirements
Several states are now requiring non-sterile compounding accreditation. This requirement is likely enforced by State Boards of Pharmacy and possibly Accreditation Organizations. It's important to be aware of the accreditation criteria in your state.
While some pharmacies work with insurance carriers, it's vital to note that compounding is primarily a cash-based business, but some insurance companies are requiring compounding compliance if the practice is occurring in the pharmacy.
Impact on Current Clients and Non-Compliant Pharmacies
For current clients of R.J. Hedges & Associates with an established compounding program, the focus is on reviewing policies and procedures to align with the updated regulations. Many new policies and forms have been added, reflecting changes in USP <800> and <795> standards. Be sure to log into the Compliance Portal® to review these items.
On the other hand, non-compliant or non-client pharmacies that haven't addressed the new regulations will need to start from scratch. This involves creating a dedicated space for pharmacy compounding and ensuring all policies and procedures are updated with USP <800> and <795> standards.
What does my pharmacy need to do?
Hazardous Drugs USP <800> has been enforceable for many months, but some people are still surprised when their State Board of Pharmacy asks for items pertaining to it. USP <800> has items for both retail pharmacies and compounding pharmacies. This section has some notes for everyone regardless of if you are retail only or do compounding, have one of our programs, or are trying to do it alone.
There is clearly a lot of confusion on what pharmacies need to have in place so here are three scenarios to help determine what you may need to be doing with some solutions that we happen to offer.
Scenario #1: I am a retail pharmacy that does NOT do compounding (at all, ever!), but I do have HDs on my shelf for dispensing.
Requirements: You DO need to have policies and procedures in place for dispensing the HDs that are on your shelves. We recommend segregating them to make it easier for the staff to identify. You must have a Completed Assessment of Risk for each item (unless you plan to store and dispense from within a negative pressure room) and you must use separate counting tools that are ONLY used for working with HDs. These counting tools should be cleaned after every use.
Solution: The R.J. Hedges & Associates Hazardous Drug Program has everything your retail pharmacy needs for dispensing drugs that are found on the NIOSH list. We also offer Completed Assessments of Risk for every HD on the NIOSH List that is found in retail pharmacies. These Assessments of Risk are ready for your review and implementation.
Scenario #2: I am a compounding pharmacy, but I do NOT compound HDs, ever.
Requirements: If you have a retail segment that dispenses HDs, you need to follow the USP <800> Hazardous Drug requirements of a retail pharmacy (read above) and, since you don’t compound HDs, good news, you do not need to worry about making your compounds in a negative pressure room! But, you still need to have processes in place to comply with 9 chapters in USP since they all deal with compounding.
Solution: The R.J. Hedges & Associates Compounding Program has everything you need to comply with requirements from your state board of pharmacy and insurance companies pertaining to USP <7>, <51>, <795, <800>, <825>, <1075>, <1112>, <1160>, <1163>, <1160>, <1178, <1191>, and <1231>.
Scenario #3: I am a compounding pharmacy that compounds HDs.
Requirements: Bless your hearts because you have all the requirements to deal with. Compounding HDs can only be done in a negative pressure room where everyone has their own fitted respirator and everyone is wearing the correct Personal Protective Equipment (PPE) based on the drugs’ Safety Data Sheet (SDS).
Solution: The R.J. Hedges & Associates Compounding Program has everything mentioned in Scenario #2 and already has a USP <800> chapter tucked in to help with those HDs.
Retail Non-Compounding Pharmacies
USP <800> changes aren’t only for compounding pharmacies. Retail non-compounding pharmacies must also adapt to some key changes. These changes include identifying hazardous drugs, having completed assessments of risk, employee training, and the disposal of hazardous drugs and soiled items.
1. Identifying Hazardous Drugs
These pharmacies must identify HDs within their inventory. We recommend you store them separately to make it easier to identify which drugs need handled with separate counting tools.
2. Assessment of Risks Conventionally Manufactured HD Products
At the completion of the HD inventory, an Assessment of Risk for Conventionally Manufactured HD Products Conducting is prepared for each HD by the state (form) the product is being dispensed. The assessment contains information such as: the HD Table, whether the product is dispensed inside manufacturer’s packaging, containment strategies and/or work practices, personal protective equipment that may be required, and is required to be signed and verified each year. If the pharmacy does not maintain an Assessment of Risk for the HD, then that HD cannot be stored within or dispensed by the retail pharmacy.
3. Employee Training
Employee training is paramount to ensure safe handling. PPE should align with SDS recommendations for each drug.
Staff needs to be trained on the risks of handling HDs, as well as the pharmacy’s procedures on storing and dispensing.
4. Disposal of Hazardous Drugs and Soiled Items
The disposal of lightly soiled PPE depends on interpretation but, generally, it's not considered hazardous waste within a community pharmacy setting. However, when HDs are spilled and items like pads are used for containment, they should be treated as hazardous waste.
It's essential to consult state and local regulations and hazardous waste companies for guidance in these cases.
Hazardous Drug Compliance for Compounding Pharmacies
Compounding pharmacies engaging in the preparation of HDs must prioritize compliance with USP <800> regulations. Ensuring adherence to these standards is not only a legal obligation but a critical measure to safeguard both employees and patients.
The implications of non-compliance can be severe, ranging from financial liabilities to criminal charges for owners and the Pharmacist-In-Charge. Precedents exist where injuries resulting from inadequate safety measures have led to legal consequences. While state boards of pharmacy may vary in their enforcement of USP <800>, the guidelines serve as an important tool for attorneys when issues arise.
Investing time and effort into full compliance is crucial. It is more prudent to establish correct and safe procedures initially, as opposed to risking the health and well-being of staff or patients, and the potential jeopardy of the pharmacy. Compounding pharmacies must adapt to key changes, including:
Containment Primary Engineering Control (C-PEC) (aka Negative Pressure Room)
Compounding HDs necessitates a dedicated negative pressure room for storage, and compound preparation.
Personal Protective Equipment (PPE)
Adherence to drug SDS is paramount, requiring the use of appropriate PPE such as gowns, gloves, head/hair/shoe covers, eye/face protection, and respirators.
Respirators
Personally fitted respirators are mandatory for individuals and must be fitted by a certified respirator fitter, initially and annually Strict adherence to manufacturers' specifications for storage, cleaning, and maintenance is essential.
By proactively implementing these measures, compounding pharmacies can not only meet regulatory requirements but also prioritize the safety and well-being of their personnel and patients.
EPA's Role
The Environmental Protection Agency (EPA) has played a surprising role in simplifying aspects of HD handling and waste disposal. This unusual partnership with a government agency aims to streamline the processes, making compliance more manageable for independent pharmacies.
Navigating Compounding Compliance and Special Scenarios
In the world of pharmacy compliance, it's not just about following the established rules. Sometimes, you encounter unique scenarios that require a different approach to stay in line with regulations. Let's delve into some of these special cases and how to handle them.
Compounds that were not picked up and Preparation Errors
Imagine you've compounded a medication for a specific patient but, for some reason, it's not picked up. Alternatively, there could be an error in the mixing and preparation process. In both cases, you need to act cautiously, these medications should be quarantined. This means you store them separately from your other inventory and dispose of them according to your company’s procedure and the processes established with your returns company or waste disposal company.
Collaborating with Returns Companies
It's important to ensure that the returns company you choose can handle your specific needs and the unique situations discussed earlier. It's vital to inquire whether your returns company provides HD disposal and to understand their specific process. Depending on your returns company's policy, they may offer to take these compounds, ensuring proper disposal for HDs including things like trace chemotherapy items. Disposal containers go by the following color system:
- Yellow Bags and Containers - Regulated Medical Waste
- Red - Bio Hazards
- Black - Hazardous Waste Pharmaceuticals
Training Your Team
Proper training for your pharmacy staff is essential. This includes:
- Use of Personal Protective Equipment (PPE): Ensure your team knows how to use PPE correctly and that it aligns with Safety Data Sheet (SDS) recommendations for each HD.
- Handling Medication Returns: Staff should be trained in the proper procedures for handling compounds that have not been picked up or preparations with errors.
- Annual Training: Some aspects of the compounding process, such as the use of certain equipment, should be refreshed annually, while others can be on a two-year cycle. Training materials, including operator manuals and internal standard operating procedures, should be part of this process.
The Role of Policies and Procedures
Policies and procedures are the backbone of compounding compliance. It's essential to understand the distinction between policies and procedures (P&Ps) and standard operating procedures (SOPs):
- P&Ps: These are the documents that follow the regulations and guidelines. They're more rigid and change only when the rules change.
- SOPs: These are fluid and describe how you specifically perform processes in your pharmacy. They can change more frequently based on the efficiency and effectiveness of your internal operations.
A solid understanding of these documents and how to create them is critical for maintaining compliance. Please know that there is a clear difference between these 2 items, they are both important for different reasons. Please note that SOPs are how your facility completes specific tasks and operations per your staff, your equipment, your process. The P&P defines a rule or regulation, who is expected to do it, and how they are expected to do it.
Documentation Requirements
For proper compliance, your pharmacy should maintain meticulous documentation. Here's what you need:
- Master Formulation Record: If there isn't an existing formula or monogram (recipe) for the compounds you make, you must create your master formulation record.
- Compounding Record: This is akin to a verification of the recipe and documents exactly what goes into each compound you create.
Both the master formulation record and compounding records are required for regulatory compliance. These documents are organized by patient and should be available for review. These records can be contained within a software program, scanned files, or paper hard copy. Electronic files and data must have an active backup in place.
The Future of Compounding Compliance
One major development in the world of compounding is the upcoming release of the Certification for Hazardous Drug Handling (CACH) from ACHC. This is a significant achievement and, once it's available, it'll further highlight your commitment to safe compounding practices. The certification is currently in the review and vetting process, and it's expected to be ready for use in the near future.
ACHC standards were incorporated within the R.J. Hedges & Associates Compounding Program in the Fall 2023 release. In Spring 2024 R.J. Hedges & Associates became the first company to have an ACHC Product Certification for their Compounding Compliance Program. This means that clients utilizing their program will benefit from the evaluation and review process that has verified the program is in compliance with ACHC’s requirements for the Non Sterile Compounding section of the ACHC standards. R.J. Hedges & Associates clients will receive a discount code for ACHC accreditation, and can expect a shorter timeframe to have applications prepared and reviewed.
Ensuring Your Pharmacy's Compliance with USP <800> and <795> Regulations
Independent pharmacy owners should always be prepared to adapt to changes in regulations and, sometimes, unique scenarios that require a different approach. Staying informed, investing in staff training, and meticulously documenting your processes are key components of maintaining compliance. While it's a challenging field with evolving standards, the commitment to safe compounding is essential for the health and safety of patients and the success of your pharmacy.
How can R.J. Hedges & Associates Help?
Understanding and adhering to HD compliance and compounding compliance is crucial for independent pharmacy owners. Staying informed about these evolving regulations and implementing the necessary changes will help ensure the safety of your patients, employees, and the overall success of your pharmacy.
Recently, NABP has told all the State Pharmacy Boards they can interpret and enforce USP <795>/<797>/<800> however they want to because there is no federal requirement. The FDA’s Food, Drug, and Cosmetic Act (FD&C Act) establishes the compounding requirements that are referenced in the first chapter of the USP Compendium. If the pharmacy listens to their state board stating that these rules are optional, both the pharmacy and the state board are 100% liable if an employee or patient is injured.
At R.J. Hedges & Associates we have a variety of compliance solutions for retail pharmacies and compounding pharmacies. The Compounding Compliance Program has been recently updated to meet all new regulatory changes and incorporated ACHC standards. With over 100 Policies & Procedures, and over 60 support documents, it has everything you need to comply with regulations, satisfy inspectors/auditors/surveyors, and provide documentation to any regulatory agency. Chat with one of our Compliance Strategists today to see which option may be best for your pharmacy.